.png)
DOUBLE SLIDER TYPE VERTICAL INJECTION MOULDING MACHINE


SV ds
DOUBLE SLIDER TYPE VERTICAL INJECTION MOULDING MACHINE
Double slider type vertical injection moulding machines are recommended when there are multiple inserts or multiple heavy components, and higher production requirement.
The 2 station sliding table moves the bottom half of the mould in and out of the clamping area on either side of the machine where 2 operators are stationed, working on their bottom half of the mould.
The 2 station sliding table is electronically operated, which increases the operational efficiency of the machine while also increasing production output.
DOUBLE SLIDER
Equipped with an two station sliding table that is electronically operated for better power efficiency and highest level of precision, while also increasing production output of the machine.
ERGONOMIC DESIGN
With slide table the mould moves out of the clamping area and closer for the operator making it much more easier for the operator to unload and load components.
4 TIE ROD
Equipped with 4 tie rod clamping unit for smooth and stable clamping unit movement, precise clamping control and eliminating all the vibrations, providing uniform distribution of clamping force inside clamping area.
RAM TYPE CLAMPING
Clamping unit is equipped with a ram type clamping cylinder which provides fast adn stable clamping pressure, while also being totally maintenance free, providing better control of clamping unit and increased mould safety
HIGH SAFETY
In addition to all the standard safety features and devices As the mould moves out of the clamping area, the operator is working outside the clamping area which increases operator safety
ADVANCED CONTROLLER
Equipped with LNC controllers which are easy to operate while providing advanced features as standard, such as detailed production tracking, machine operational statistics, remote monitoring and control, user profiles, Automation integration, Industry 4.0 devices integration, and much more.
GREENDRIVE
Greendrive hydraulic system is also available, which provides higher machine efficiency, silent machine operation, better accuracy, reduces machine operational temperature, and increases machine's service life.
HIGH PRODUCTION
With two station sliding table there are 2 operators working on the same machine reducing the idle time of the machine, and increasing the production output by almost 1.6 times other machines.
MADE IN INDIA
Designed, engineered and manufactured in India, which translates to better machine quality and higher trust, for customers, it is beneficial due to our big service network, better support, and stronger availability.

INSERT MOULDING
With the vertical design of the machine, it gets really easy to insert mould components as the inserts stay locked in their place and you get perfect insert moulded components.
When it comes to inset moulding Vertical Injection Molding Machines are the ideal choice for many solutions, in the case of overmoulding inserts, precision is a premium. With its compact, design and vertical clamping unit, User-Friendly Controller and easy setup procedure,
Double Slider Type Vertical Injection Molding machines can provide the best results for medium volume production requirements.
_edited.png)
FAST AND STABLE CLAMPING PRESSURE
All Double slider type vertical injection moulding machines use the ram-type clamping unit.
There are significant advantages of ram-type clamping unit over the conventional toggle-type clamping unit, such as
-
No extra maintenance is required.
-
No need to regularly lubricate or grease the clamping unit.
-
No regular complete cleaning is required.
-
Longer operational life.
-
High accuracy and precision.
-
Better distribution of clamping force.
-
Better control over clamping unit pressure and speed settings.
-
Stable clamping pressure.
-
Fast and smooth clamping unit operation.
-
Increased mould safety.
Designed for high stability and reliability, all the machines are designed with four tie-rod style clamping unit for stable and vibration-free clamping unit movement, four tie-rods provide high structural strength and smooth operation.
Ram type clamping unit combined with four tie-rod type clamping unit, translates to a better distribution of clamping force over the mould, providing a better moulding result.
.png)
DIVERESE INJECTION UNIT
The injection is the only way to control material flow inside the mould thus higher control over material flow and injection position is required to achieve high-quality moulded components.
With a highly customizable injection unit you can choose the injection unit that suits your production requirements.
Using an accurate measuring apparatus and highly sensitive controller we can accurately control the positioning of injection to control the exact amount of material entering the mould thus producing the best moulding results and these results can be reproduced an infinite number of times.
The Hydraulic injection system is highly reliable and robust with our optional bimetallic screw injection unit and can be taken to next level of usage with high-density materials.
Multiple Heating Zones provide accurate control over the material melting process inside the barrel, you can set custom heating stages for materials and melt the material accurately resulting in reduced time material has to stay at higher temperatures thus preserving material composition and integrity.
Multiple Injection Unit Screw Options depending on your production requirement you can choose your ideal injection unit.


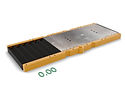
FAST AND PRECISE SLIDE TABLE
Double slider machines are equipped with a 2 station sliding table that slides the bottom half of the mould in and out of the clamping area, from the left and right operating sides of the machine.
There are two operating station on the machine, left and right operating station. when the slide table is at left station mould mould at right side is inside the clamping area carrying out moulding process, once the process is completed and the operator at the left station has finished his work and starts the next cycle the mould form left station moves inside the clamping area and the right side mould moves out of the clamping area containing finished moulded parts, the operator at right station removes the moulded components and loads new inserts and starts the next cycle continuing production process.
With the help of two station and two moulds the production cycle time and machine idle time is greatly reduced resulting in increase of production by up to 1.6 times compared to single slider and fixed type of machines.
The slide table is electronically controlled resulting in increased operation accuracy, and increased operational efficiency, with high positioning accuracy machine ensures that the mould is perfectly in its place before closing the mould, thus eliminating the chances of mould damage while mould closing.
.png)
CONTROLLER
All our machines come equipped with LNC controller as standard.
LNC controllers are best in the segment, they provide a high level of control and precision and advanced features that many controllers in this segment can not provide.
We have two controllers depending on the machine model that you choose
In5800 - LNC controller with an 8-inch HMI display and similar performance to the other higher-end LNC controller.
In6800 - LNC controller with a 10-inch HMI display, high-end features, and top of the line performance.
Both controllers have advanced features for machine control and user inputs while being user-friendly and easy to operate.
Equipped with features like remote diagnostics for problem resolutions, EUROMAP configuration, remote monitoring, inter-machine data compatibility, customizable functions, easier integration for automation devices such as robots, Easier integration of industry 4.0 technology, and much more.
We also provide other controllers depending on our customer's requirements but we recommend LNC controllers with our machines over all other controllers.
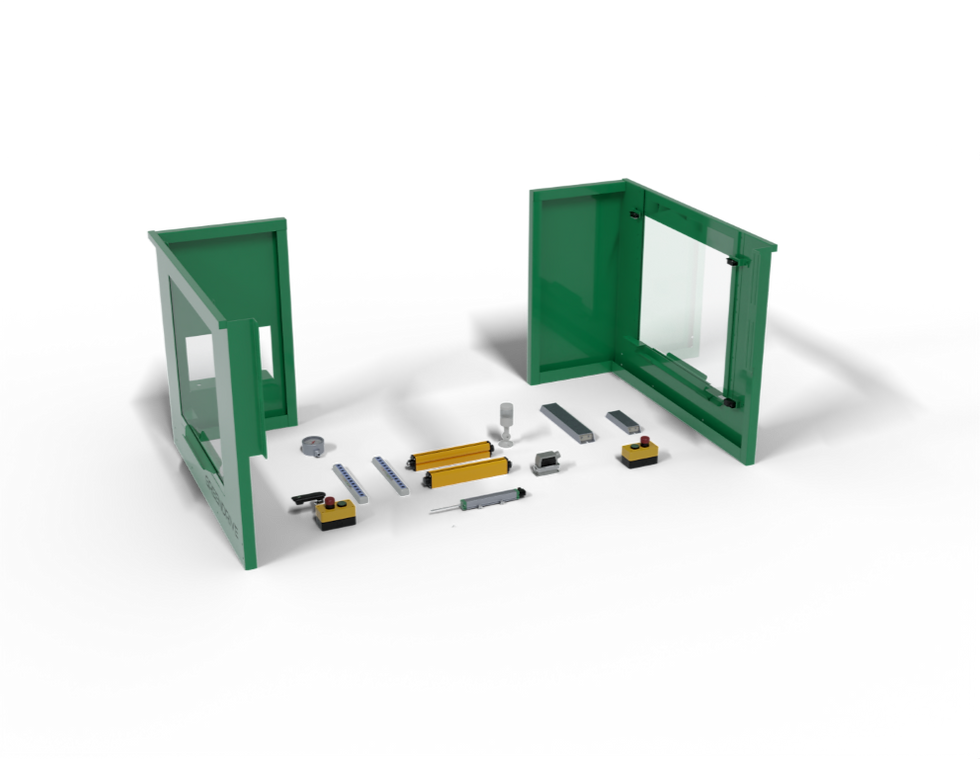_edited.png)
SAFETY IS HIGHEST PRIORITY
When operating machines that are designed to operate at high temperatures and pressure, safety should be the highest priority, with our machines safety is a core part of the design as we have integrated multiple safety features in our machines to reduce the number of accidents to zero.
Equipped with multiple safety devices such as.
-
Safety light curtains
-
Side safety doors
-
Emergency switches
-
mechanical pressure indicators
-
electrical redundancies
-
electrical safety
-
emergency light with buzzer
-
mechanical safety for mould and machine safety.
All safety devices work together to create a totally safe operating experience for the operator, reducing the chance of accidents to almost zero.
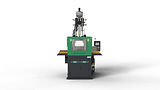
MACHINE OPERATION
-
CYCLE START
-
SLIDE IN
-
MOULD CLOSE
-
MOULD SAFETY STAGE
-
CLAMPING
-
INJECTION
-
COOLING START
-
PLASTICIZING
-
SUCKBACK
-
COOLING STOP
-
CLAMPING RELEASE
-
MOULD OPEN
-
SLIDE OUT
-
EJECTION
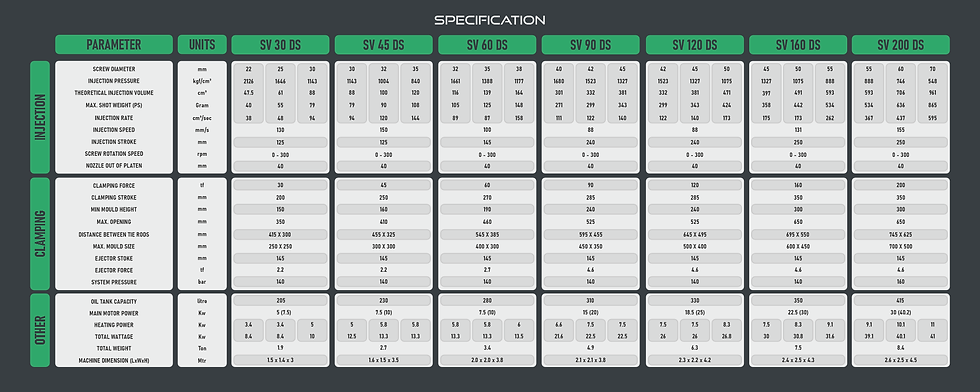
MACHINE PHOTOS
SUPPORT FOR DOUBLE SLIDER TYPE MACHINES
Looking for resources or support for a double slider type vertical injection moulding machine, visit our support page for all the resources.